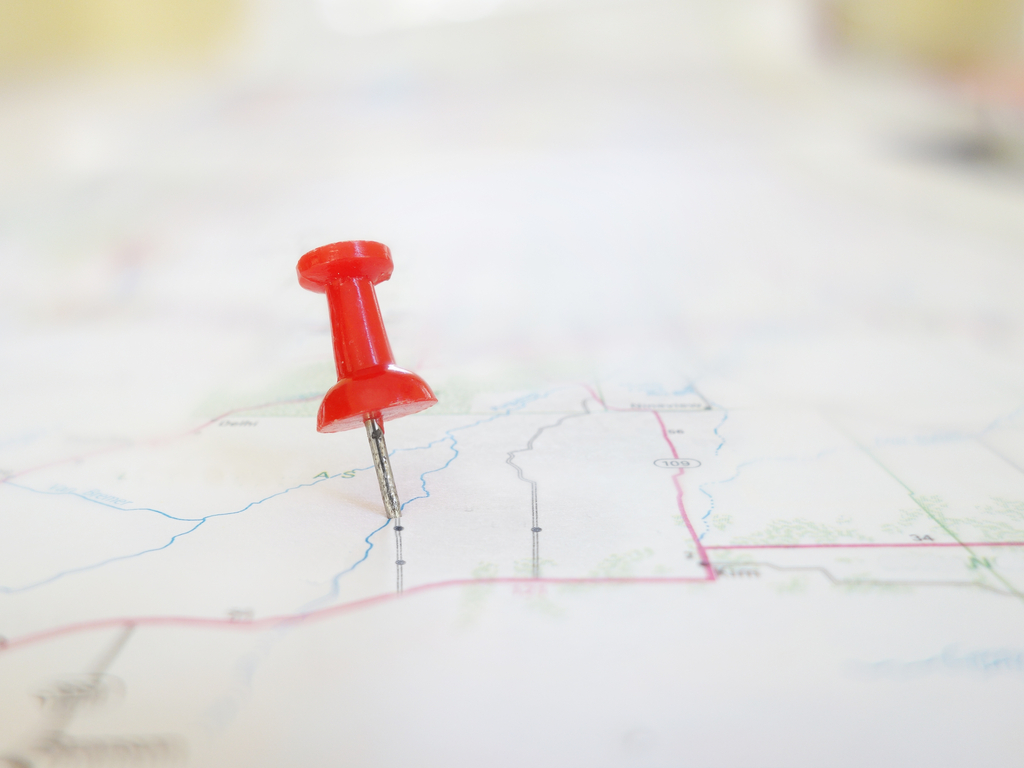
[…] Professor Martin Christopher tells us why he thinks there will be a shift away from global sourcing strategies
A few years ago, there seemed to be an unstoppable march towards global sourcing. The race was on to find ever-lower cost sources before your rivals, in what was very much a case of everyone on the bandwagon. But with the advent of new technology and a growing demand for next-day delivery from consumers, is the field about to shift once again? Is there an alternative to global sourcing? Is it even relevant? We spoke to Professor Martin Christopher to find out what he thinks, and to see how the supply chain is evolving.
Shifting sands
Looking at the origins of current practices, the big move to global sourcing began maybe 30 years ago because of low-cost country sourcing. Whole industries moved offshore. As an example, Marks & Spencer made a virtue out of sourcing locally. Everything they sold they made in the British Isles. They then found it increasingly difficult to compete with some of the newcomers on the high street pricewise. They had to move offshore. Marks & Spencer reversed almost 100 years of heritage, cut ties with historical suppliers and moved much of their sourcing overseas, which was typical of a lot of companies. The strategy stemmed from a very narrow definition of cost: what does it cost me to buy at the factory gate and the cost of delivery? If the price was less than they had been paying locally, they were happy. The only aspect they didn’t consider was the massive increase in lead times at the same time the high street was becoming increasingly fashion oriented. When you had lead times of around 12 months, it became increasingly difficult to be competitive.
Working smarter
Now, we’re a little smarter. We look at the total costs of ownership, the cost of financing the supply chain, all the risks and likely quality problems. Some companies began re-shoring – but that wasn’t practical in so many cases. Factories had been shut down, they’ve been built over, the skills have gone, and the knowledge lost; so, my view is rather different.
I believe we should take a move toward what is known as local for local – which means wherever demand is, that’s where I’d like my supply to be. Increasingly, that’s becoming more and more of a practical solution because of the number of revolutionary changes that are taking place in manufacturing where we can make things in smaller quantities.
The thinking was until recently that you wanted to centralise, get the economies of scale, have a mega factory that pumps the stuff out and that has been received wisdom for quite some time. Now with 3D printing and a whole host of other technology, it’s becoming possible to have a much more fragmented manufacturing and sourcing strategy.
It’s not necessarily about bringing manufacturing back; it’s putting it where it’s needed. The long-term implications for the shipping industry are interesting because if people follow my way of thinking, we’ll be moving less stuff around the world. Raw materials, chemicals and crude oil will continue to move, but the idea we move container loads of goods from one place to another isn’t necessary because we can print them or produce them locally. It’s the way I see the future moving. Rather than re-shoring or near-shoring, I think the word is right shoring. We put it in the place where it’s needed. Obviously, we’re constrained because you can’t necessarily source everywhere you would like to.
Cultural shift
Increasingly, we’ll be driven down this road because long lead times are a killer in a market that is fast moving. We have customers that want an immediate response. We see it in the consumer market. People’s expectations are changing because some goods permit same day or next day delivery. You can’t live with a six-week lead time under those circumstances.
There is a demand for a much more rapid response, and that’s what’s driving a lot of this rethinking. The true cost of the supply chain is the cost of not being able to meet the demands of the marketplace. The only alternative is to carry an inventory, which isn’t possible for many companies, especially now that we have an increasingly technical capability.
Wherever you can put a 3D printer, you can produce something. Your inventory is electronic and in the form of a blueprint. The vision for many companies is that you are carrying less of a physical inventory in central locations and making it when you need it. It’s not science fiction to think in ten years you will be using drones to carry 3D printed spare parts to ships.
This article was originally published in the Marine Trader, IMPA’s official journal for maritime procurement and supply chain management, in issue 05 of 2017. Head over to www.impa.net to find out more or simply read new issues on the go with the MT Journal app.